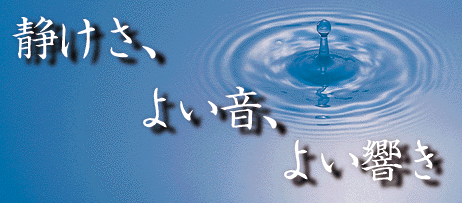
Title means "Quietness", "Comfortable Sound" and "Excellent Acoustics"
Nagata Acoustics News 99-5iNo.137j
Issued : May 25, 1999
Amuser Kashiwa's Crystal Hall Opens
by Chiaki Ishiwata
Exterior View
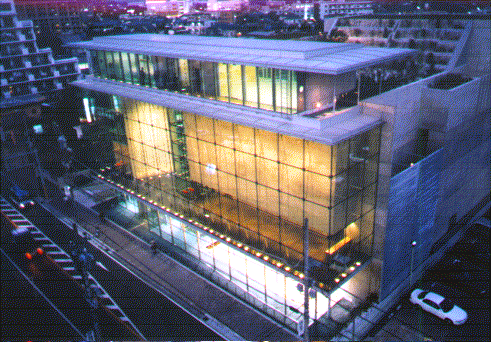 |
In January 1999, a new facility with a 400-seat multipurpose hall opened for use in Kashiwa City. Kashiwa City is a Tokyo bedroom community with a population of 320,000. It is located approximately 30 minutes northeast of Tokyo's Ueno Station on the JR Joban Rail Line. The new facility, named "Amuser Kashiwa," benefits from an excellent location, just a short, five-minute walk from Kashiwa Station and adjacent to a shopping area that draws large numbers of weekend shoppers.
Amuser Kashiwa fits right in with the perennially festive atmosphere of Japan's department stores and shopping arcades nearby. While the structure's exterior is primarily exposed concrete, "dot-point grading" (DPG) treated glass paneling on its front side enlivens and brightens the building's appearance and atmosphere.
Amuser Kashiwa replaces an aging civic culture facility that had stood on the same site. In planning the new facility, it was decided to add a multipurpose hall as well as other functionalities now expected in a culture facility. Architecture designer was selected through a process of competition. NIHON SEKKEI Inc. were responsible for the the project's design and project management work, and a consortium of companies led by TOKYU CONSTRUCTION Co., Ltd. were responsible for the construction.
<< Inside Amuser Kashiwa >>
Inside Amuser Kashiwa are the following rooms and facilities:
* "Crystal Hall" -- a 400-seat multipurpose hall.
* "Plaza" -- a gallery/lecture space with a level floor.
* A sound- and vibration-proof rehearsal room for all kinds of rehearsals.
* A 3-story-high central atrium.
* Rooms for public use, including a:
Cooking demonstration room;
Ceramic arts room with its own kiln; and,
7 Meeting rooms. (One of these is a Japanese-style Tatami room).
Rooms for public use have floor-to-ceiling glass paneling both for the walls that face the outside of the building and the walls that face inward to the atrium. In addition to creating a bright, naturally-lit indoor environment, this design makes the lively activities and goings on in each of the rooms visible both to passersby outside Amuser Kashiwa and to people in the atrium area.
<< The Rooftop Garden >>
Amuser Kashiwa uses its entire lot for its structure. To add greenery, man-made soil was brought to the rooftops of the third through fifth floors, then live plants were added to turn them into rooftop gardens. Looking out the window from the meeting room on the top (fifth) floor, it is easy to forget that one is in a city. All that the eyes can see is the green foliage of the rooftop garden and the blue sky up above!
<< Crystal Hall >>
Hall Interior View
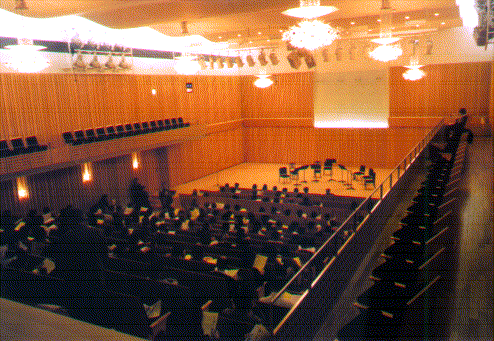 |
Crystal Hall responds to the needs of Kashiwa City's local groups and organizations. Because this city is especially rich in musically-oriented groups eager for a place to perform, we designed the hall to have a shoebox configuration when the stage's movable reflection panels are deployed. In addition, for the hall's interior walls, we used wood paneling that features narrowly ribbed finishing for enhanced acoustics. Beautiful chandeliers overhead complete the concert hall mood. For multipurpose use, the stage's reflection panels can be removed and the stage has been fitted with a curtain.
Because of the small size of the hall, one of the aims of our acoustical design was preventing the sound reflections from reflecting back into the audience seating in an unpleasantly harsh manner. With this aim in mind, we selected a randomly ribbed finishing for the walls and gave a curved shape to the ceiling to create the dispersion characteristics we desired. Also, at the central bottom portion of the stage's rear wall, we used openwork rib paneling and installed a retractable curtain behind it. By adjusting this behind-the-scenes curtain, the hall's reverberation time can be adjusted depending on the musical instruments used and performers' preferences.
In its shoebox configuration, at 500 Hz and a full audience, Crystal Hall's reverberation time is 1.2 seconds. Take off the stage reflection panels, and arranged with its stage curtain, the hall measures a reverberation time of 0.8 seconds.
<< Plaza >>
The spaces allotted for Plaza and Crystal Hall are directly above and below each other. Therefore, we adopted sound and vibration isolation strategies for the Plaza space. We designed a "floating" concrete floor supported by elastic anti-vibration material and used a layer of gypsum board. We successfully achieved sound isolation for 85 dB (at 500 Hz).
With regard to vibration isolation, we gave special attention to Plaza's intended use as an exhibition space. We made sure that the rails installed for hanging exhibition panels are vibration proof and we took special care that vibrations from hanging panels or pictures would not generate unpleasant noise inside the room.
We also addressed Plaza's intended use for lectures and symposiums by inhibiting the room's reverberation time. We selected punched metal and GW materials for the room's walls and GW backed by a layer of open space for the ceiling. These measures created an environment where sound is absorbed, creating the appropriate reverberation time for lectures and other speech-based uses.
Now that the city has Crystal Hall, there will be even greater opportunities to hear good music played, and Amuser Kashiwa has the space for its budding musicians to practice all they please. To me, this sounds like a sure recipe for more musicians making a name for themselves--from Amuser Kashiwa to all of Japan--and beyond!
Amuser Kashiwa's address is 6-2-22 Kashiwa City, Chiba Prefecture, JAPAN
Renovation of St. Margaret's Chapel
by Akira Ono
St. Margaret's Chapel
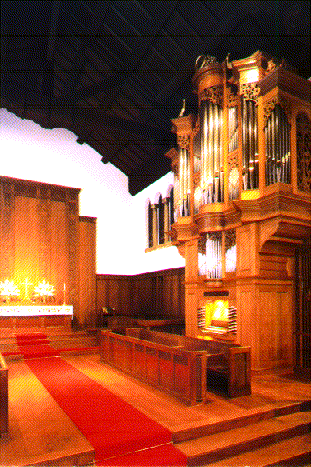 |
St. Margaret's School is an all-girls high school located in the quiet, upscale Tokyo suburb of Kugayama, in Suginami Ward. The school is associated with St. Paul University, a well-known, Jesuit-founded university, also located in Tokyo.
The school's St. Margaret's Chapel was built some 70 years ago and included a pipe organ. However, the pipe organ deteriorated over time. The school decided to replace it with a new pipe organ and commissioned Taylor & Boodie, a U.S. organ builder located in the state of Virginia, to build the new instrument. Taylor & Boodie requested adjustments to the chapel's room acoustics so that the new organ would sound its best. The school asked Nagata Acoustics to consult on the renovation project for this purpose.
Before the project began, the chapel's reverberation time measured 1.4 seconds at 63 Hz, and 1.8 seconds at 500 Hz and 1 kHz. That is, the reverberation time was shorter for low register sounds.
<< Improving Acoustics within the Constraints of a Historical Landmark >>
The immediate challenge we faced on this project was the school's requirement that the chapel not be altered at all visually. St. Margaret's Chapel has historical value that the school wished to preserve. To accomplish this difficult task, we enlisted the help of Nobuyuki Ebihara to carry out the adjustments we would design.
Mr. Ebihara is the chief master craftsperson of Ebihara Komuten. His specialty is the fine sukiya-style construction used in traditional Japanese tea houses. His attention to detail is impeccable, and we often call on him to build the 1/10 scale models we use in our acoustical design process.
<< A Strategy to Address the Sound-absorbing Wood Walls and Floor >>
The framework of the chapel building and its floor are entirely made of wood. Moreover, the area around the altar is wood paneling. Upon investigation, we confirmed that the vibrations of these wood elements were absorbing the low register sounds. Because the pipe organ is installed at one side of the altar, we determined that strengthening the walls and floor of the altar area would be an effective strategy to improve the chapel's acoustics.
<< Strengthening the Walls around the Altar Area >>
We removed a piece of wall paneling from the altar area to learn about the wall's construction. We discovered that the panels were made of oak, each approximately 40 cm (15.75 inches) in width and approximately 4 cm (1.6 inches) thick. Each panel was supported by a brace, and was kept in place by a narrow top beam decorated with delicate carving. Between the chapel building's frame and the panels was space filled with nothing but air. Therefore. we devised a plan to fill in the space between the structure's frame and the paneling, as we knew that this would stop the wall panels from vibrating and absorbing low register reverberations. We affixed numerous layers of gypsum board to both the chapel frame and the frame-facing sides of the oak paneling. Then we filled in the small remaining crevices with a gypsum-based adhesive.
<< Strengthening the Wood Floor >>
The original Chapel floor was made of oak boards supported by joists. The substructure was Japanese-style wood joinery, with the wood spaced at 40 cm intervals. To strengthen the floor, we used adhesive and screws to affix 8 mm (0.3 inch) gypsum board to the underside portions of the wood boards in-between the floor joists. We layered the gypsum board, putting between 4 and 8 layers under each oak floorboard, and we added additional vertical supports between the substructure and the oak floorboards as well.
<< Laborious Hot Summer Work >>
The work of adding gypsum board under the chapel floor required a huge amount of material and much human labor. We embedded 600 gypsum boards, each weighing 15 kg, under just the altar portion of the chapel's floor. The only entrance to the floor's substructure was via a ventilation opening 60 cm x 40 cm (24 inches x 16 inches). Both the workers who performed the job and their materials crawled through this space.
The renovation work was scheduled during the school's summer vacation, so the workers suffered through the summer heat and fought off the bugs as they worked. This was in addition to the grueling labor of pushing up each gypsum board from a half-crouching position to affix it to the underside of the chapel's floor. I have no doubt that this was truly hard work, but the results of the excellent workmanship were securely attached gypsum boards that serve their purpose well. Walking inside the chapel now feels like walking on a slab of concrete, in striking contrast to how the flooring felt before the renovations.
<< Installation Preparations for the New Pipe Organ >>
Preparations for the installation of the new pipe organ progressed in the following stages:
1. Complete the interior wall strengthening renovations.
2. Dismantle and remove the old pipe organ from the chapel.
3. Complete the floor strengthening renovations.
4. Move and reinstall the chapel pulpit
5. Build a partition in the blower room for the new organ.
During these installation preparations, the organ builders back in Virginia sent drawings for the project, as well as requests for the desired acoustical conditions in the area near where the pipe organ would be located. It was Nagata Acoustics' responsibility to interpret the documents and information received from Virginia and give specific instructions to Mr. Ebihara.
<< Preserving Parts of the Old Pipe Organ >>
The front grating of the old pipe organ was decorated with Japanese "sukashi" openwork carving that the school wanted preserved and used in the construction of the new organ. In addition, any of the pipes from the old organ that could be reused were also to be incorporated into the new organ. Extra care was exercised in dismantling these parts of the old organ, which were then packed and shipped to Virginia.
<< Repositioning the Altar >>
In connection with the installation of the new organ, the Chapel's altar required repositioning. This altar is an incredible work of art decorated with fine carving over its entire surface and weighing approximately 230 kg (506 lbs). We dismantled and reassembled the altar with the utmost care, and turned it around from left to right.
It was necessary to replace the altar's door. Like the body of the altar, the original door was lavishly decorated with intricate carving, and the new door, too, needed to be decorated in the same manner. Mr. Ebihara had the task of finding a craftsperson capable of this effort. After considerable searching, word of mouth led us to Kanzaburo Ono. At the time we first met Mr. Ono, he was already a venerable 83 years old. Among his many illustrious credits, Mr. Ono is the last surviving carver from among the craftsmen who produced the wood carvings on Japan's national Diet building. He continues working and producing fine carvings to this day.
Once we approached Mr. Ono about the chapel altar door project, he came to St. Margaret's to see the altar and its decorative carving. His reaction confirmed our own admiration for this Western-style wood carving wrought by Japanese craftsmen in an era--many years ago--when contact with Europe and the United States had barely begun. Mr. Ono placed his hands on the altar and lovingly traced the workmanship with his palms and fingers. He accepted our commission and proved that our trust in his abilities was well placed. The door that he carved for us so perfectly matches the altar that it is impossible to distinguish his workmanship from the rest of the altar, which is all original woodwork from the chapel's earliest days.
<< Changes in the Reverberation Time >>
The most notable acoustical change before and after the renovations, was the lengthening of the reverberation time at the 63 Hz frequency. Before the renovations, it was 1.4 seconds. With the old organ removed and the renovations completed, the reverberation time for this frequency measured 2.5 seconds. After the installation of the new organ, the reverberation time measured 1.9 seconds. By comparison, the renovations had virtually no impact on frequencies above 125 Hz.
<< Documenting the Renovation Work >>
Old structures such as St. Margaret's Chapel inevitably require renovation work from time to time. This time, our renovation work focused on adding strong fortifications behind the interior walls and underneath the chapel floor. But there will undoubtedly be other renovations sometime in the future. To provide resource materials for that eventuality, Mr. Ebihara wrote a detailed report documenting all aspects of the renovation project and provided it to our client, St. Margaret's School.
<< Unveiling Held a Full Year after Installing the Organ >>
In April 1998, less than two years after the summer of 1996 (when we began the renovation work), the installation of the new organ in the chapel was complete. However, St. Margaret's School followed the request of the organ builder and gave the organ a full year to be used and adjusted to its surroundings before holding a formal unveiling. During this year, the chapel and organ were used daily, giving the organ builders plenty of time to fine tune the instrument, and the instrument plenty of time to blend with the atmosphere of its home. On April 3, 1999, organist Harold Vogel performed the first recital on the new chapel organ. The rich sound of the pipe organ flowed throughout the entire sanctuary in fitting tribute to the joining together of fine craftsmanship of yesterday and today in this historic Tokyo landmark.
"Three Great Tenors" Concert at Tokyo Dome
by Yasuhisa Toyota
Just a few months ago, I had the opportunity to attend a "concert" by the "Three Great Tenors," at Tokyo Dome, a roofed baseball stadium. The concert received a great deal of advance media attention, as did a similar concert at Yoyogi Stadium (another enclosed sports arena in Tokyo), three years before. While I had heard many comments about the earlier concert, this was my first opportunity to hear these three famous singers in a comparable setting, so I attended the evening at the Dome eagerly.
<< The Setting >>
Arriving at Tokyo Dome on the evening of the event, I saw that a temporary stage was set up in a corner of the infield. Metal tubular chairs were arranged in rows on the playing field and the rest of the audience sat in the regular stadium seating above the outfield. Together, the stadium sat more than 40,000 attendees.
My seat was more or less in the center of the temporary seating set up on the infield, near the booth that had been temporarily constructed for the lighting and sound crews. This was certainly a good seat, quite possibly among the best in the "house." Nevertheless, the stage seemed very far away, and when I turned to look behind me, the outfield seating seemed even more distant. I had brought a pair of high performance binoculars with me. But even using these, the singers on stage looked minuscule. Only when I used the binoculars to look at one of the two large projection screens--set up at each side of the stage--did the singers look large enough to give me any sense of their normally impressive stage presence.
<< The Performance >>
The concert program had Domingo, Carreras, and Pavarotti each performing arias and Italian folk songs independently, a different tenor starting to sing whenever another stopped. James Levine and the Metropolitan Opera House Orchestra played "back-up." Unfortunately, the quality of the sound heard at the stadium on this evening was atrocious. It bore no resemblance to the quality of sound needed to make a performance of this kind enjoyable. If this was the best that Tokyo Dome can do, it would be far better to stay home and watch the performance on video or laser disk. Further, if this was how I reacted to the sound quality in a good seat in the center of the infield, I cannot even begin to imagine what the visual and sound experience were (or were not) for the audience in the outfield seating. The tenors' performances received warm applause, but I wonder if the audience really felt satisfied with what it heard that night.
<< The Economics >>
What is not difficult for me to imagine is how expensive it must have been to bring together the line-up of performers at Tokyo Dome that night. If the same concert was held at a concert hall, the price of the tickets would have made one's eyes pop.
Had the use of the Tokyo Dome been accompanied by the more than 40,000 tickets being sold at inexpensive prices, I would have understood why the event was held at Tokyo Dome. Inexpensive ticket prices of perhaps several thousand yen (about US$25.00) each would have been some justification for holding the event at Tokyo Dome. I would probably have considered the evening to be more in the nature of a "festival" or "event" than a classical music concert, and that would have been fine for what it would have been.
But the most expensive tickets for the Three Great Tenors Concert at Tokyo Dome cost (85,000 (approx. US$710.00). To pay tens of thousands of yen to watch the performers via a projected image and listen to them through loudspeakers is too hideous for words! Not to mention that much of the audience who paid dearly to endure the long "concert" seated in uncomfortable chairs made of metal tubing did so dressed in gala attire barely more casual than formal wear.
<< Who Is Responsible for the Quality of a Performance? >>
Responsibility for the poor acoustics and visibility at the Tokyo Dome Three Tenors Concert cannot fairly be placed on the event's sound and lighting designers or crew. The impossibility of staging a true classical music concert in that location was obvious long before these professionals were brought on board.
Some responsibility for allowing such an acoustically and visually unsatisfying event to take place rests on the shoulders of the event's producers. On the other hand, the reality is that huge numbers of people were willing to pay the high prices of the tickets, so from a business perspective the event made sense.
Perhaps some readers will think that I am out-of-bounds to even express my opinion on the propriety of offering this entertainment to the public. Perhaps this was just business as usual for the concert/entertainment industry and the question of a concert's artistic value should not even be asked.
But in my opinion, the evening's performers, including the orchestra and conductor as well as the three tenors, do bear a strong responsibility for what the audience experienced at Tokyo Dome. During their rehearsals, they were fully capable of checking both the sound and visual quality of each others' performances. They certainly knew the ticket prices that were charged. "Sell whatever the market will bear," may be appropriate for some situations in the world of business. In the performing arts, the ultimate responsibility for the quality of a performance lies with the performers themselves.
<< The Implications >>
There is no way to count the number of people in the Three Tenors Concert audience who rarely attend other classical music concerts. It seems obvious to me that there must have been many people at Tokyo Dome that night who never--or almost never--set foot in a concert hall. They decided to pay the high price for the evening's tickets primarily because of all the publicity and hype they had heard. Yet it is from this very population of novice concert goers that we should expect to draw the audiences who will fill concert hall seats regularly at classical music performances of the future. I surely hope that the experience of listening and hearing the three tenors at Tokyo Dome did not turn them off to live classical music performances before they have had the chance to sample its true artistry and listening satisfaction.
Architectural Competition for the Helsinki Symphony Hall
The city of Helsinki, capital of Finland, is now planning to build a new concert hall with 1500 seats. The hall is scheduled to be in the central part of the city and next to the Finlandia Hall designed by the famous architect, Alvar Aalto. Widely opened competition is scheduled to select the architect for the new concert hall. The competition program is available at the following internet address.
http://www.minedu.fi/helsinkimusiccentercompetition/
Nagata Acoustics Inc. has been appointed as an acoustician for the project.
Nagata Acoustics News 99-5iNo.137j
Issued : May 25, 1999
Nagata Acoustics Inc.
E-mail: info@nagata.co.jp
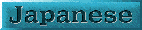